五、连杆加工工艺
1、连杆功用及结构
连杆是连接活塞与曲轴的动力功能件。连杆小头通过活塞销与活塞相连,连杆大头与曲轴的连杆轴颈相连。并把活塞承受的气体压力传给曲轴,使活塞的往复运动转变成曲轴的旋转运动。
连杆工作时,承受活塞顶部气体压力和惯性力的作用,而这些力的大小和方向都是周期性变化的。因此,连杆受到的是压缩、拉伸和弯曲等交变载荷。这就要求连杆强度高,刚度大,重量轻,连杆常用材料有QT700-2、40MnV、38MnSiV35。
连杆结构分为三部分:连杆小头、连杆杆身、连杆大头。
连杆组件的构成:连杆体、连杆盖、螺栓与螺母、衬套。
连杆的结构类型通常按结合面结构形式分为两类:
平切口:结合面与连杆杆身轴线垂直(见下图),通常用于汽油发动机。
斜切口:结合面与连杆杆身轴线成一定夹角(见下图),通常用于柴油发动机。
2、连杆工艺设计
连杆外形不规则而且较复杂,不易实现定位,大小头是细长的杆身连接,容易变形;尺寸公差、形位公差,表面粗糙度等要求较高。连杆的加工工序遵循先面后孔,先基准后其它的原则。
连杆是一个刚性比较差的零件,因此定位夹紧应减少变形对加工精度的影响。连杆加工过程之中,大多数工序都是以大小头端面、大头孔或小头孔,以及零件图纸之中规定的工艺凸台为精基准的。为保证大头孔与端面垂直,加工大小头孔时,应以一端面为定位基准。加工其中一孔的时候,通常以另外一个孔作为定位基准。
2.1主要工艺介绍
2.1.1 两端面加工
连杆的两端面是加工过程中主要的定位基准面,而且在许多工序中反复使用,所以应先加工它,并随着工艺过程的进行要逐渐精化,以提高其定位精度,大批量生产中,连杆两端面多采用磨削和拉削加工。
2.1.2 大小头孔加工
连杆大、小头孔的中心距影响发动机的压缩比,因此其中心距要求较高,一般在±0.05mm以内,这也是连杆加工中的关键工序,为保证与其他孔或平面的位置精度,精加工通常采用镗削加工,而且大、小头孔的精镗一般都在专用的双轴镗床同时进行,多采用双面、双轴金刚镗床,有利于提高加工精度和生产率。
大、小头孔加工工艺流程常为:钻→扩→粗镗→精镗→珩磨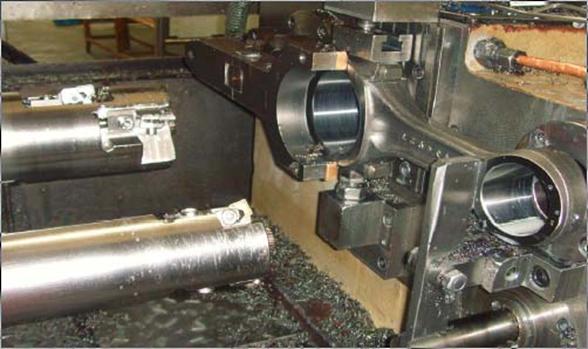
2.1.3 连杆加工的主要工艺流程
序号
|
工序内容
|
常用设备
|
1
|
铣两端面
|
专机
|
2
|
镗小头孔
|
专机
|
3
|
铣小头斜面
|
万能设备或专机
|
4
|
镗大头上下半圆
|
专机
|
5
|
钻油孔并倒角
|
万能设备或专机
|
6
|
铣断
|
万能设备或专机
|
7
|
粗磨连杆、连杆盖对口面
|
万能设备或专机
|
8
|
钻杆、盖螺栓孔
|
万能设备或专机
|
9
|
精磨连杆、连杆盖对口面
|
万能设备或专机
|
10
|
扩铰杆盖螺栓孔
|
万能设备或专机
|
11
|
铣瓦槽
|
万能设备或专机
|
12
|
杆盖配对并装配
|
|
13
|
自动拧紧
|
专机
|
14
|
精磨两端面
|
专机
|
|
|
15
|
精镗小头底孔、半精镗大头孔
|
专机
|
16
|
压衬套
|
专机
|
17
|
称重
|
|
18
|
精镗大头孔、精镗衬套孔
|
专机
|
19
|
珩磨大头孔
|
专机
|
20
|
总成清洗
|
专机
|
21
|
终检
|
|
|
3、连杆制造工艺的发展
在传统制造工艺中,连杆体和盖的制造依赖两种方法:
1)连杆体和盖整体锻造→锯切分离→接触面机加工→装配。
2)连杆体—盖分别锻造→接触面机加工→装配。
采用上述两种工艺,不仅需对连杆体和盖的联接面进行铣削和磨削,并且在该联接面上还要钻铰螺栓定位孔和攻螺纹孔,或者切制端面齿,钻铰定位销孔和钻螺栓孔等,以便将来能使连杆体 —盖实现精确合装。为此,需要较多的加工机床,经过十几道工序,耗费大量的加工工时。
针对连杆传统制造工艺中的缺点,为了降低制造费用和工时,提高配合精度,连杆断裂剖分工艺被提出,在实施断裂剖分之前,先粗镗连杆大头孔,然后在其预定断裂处加工两个对置的沟槽,为应力集中点。随后,将连杆大头孔套装到一台进行断裂剖分的装置的两个半芯轴上,并将连杆进行定位和夹紧。然后利用冲击力,将用来胀裂连杆的楔插入上述半芯轴中,此时在楔的冲击下,连杆的大头孔在沟槽处被断裂剖分为连杆体和连杆盖,这种新工艺,使分离后的连杆和连杆盖能直接在断裂面处自然精确合装,无需加工配合面,达到了减少加工工序和减少加工机床的目的。此外,除连杆剖分面具有较高的配合精度外,还由于其剖分接触面是凸凹不平的,大大提高了接触面积,从而提高了连杆承载能力。
(中国工程机械动力部件网)(完)