三、曲轴加工工艺
1、曲轴结构及材料
曲轴属细长杆件,主要由主轴颈、连杆颈、油封轴颈、齿轮轴颈组成,在主轴颈、连杆颈上有油孔,两端有螺纹孔
根据发动机的结构,曲轴主要有直列和 V型曲轴,上图为直列曲轴,主轴颈用于支撑整个曲轴,连杆颈与连杆相连,带动连杆活塞做上下往复运动根据发动机的工作状况,曲轴常用材料有:球墨铸铁、合金钢。
对于汽油机曲轴和小型柴油机曲轴,由于功率较小,曲轴毛坯一般采用球墨铸铁和优质碳素钢,常用材料有:QT700-2、45钢等;中、重型柴油机曲轴毛坯一般采用合金钢,常用材料有:48MnV、35CrMo 等。
曲轴是发动机中的重要零件,由于曲轴具有结构复杂、刚性差、技术要求高的特性,因此加工工艺难度大,而其加工质量又直接影响到发动机的技术性能和寿命,且曲轴属细长杆件零件,在加工中极易产生变形,这就需要在进行加工工艺设计时,根据曲轴的材料、技术要求、生产能力等要求,综合、全面考虑加工方案,
2、主要工艺介绍
2.1 中心孔的加工曲轴的中心孔是曲轴加工过程的重要定位基准,曲轴常见的中心孔加工方式为几何中心孔和质量中心孔。
以曲轴毛坯轴颈的外圆定心来加工出的中心孔称为几何中心孔,以曲轴毛坯的旋转质量中心加工的中心孔称为质量中心孔。由于几何中心孔的加工工艺简单、设备价格低,因此国内目前大多采用几何中心孔,但对毛坯质量差的曲轴的动平衡影响较大。
质量中心孔的加工是寻找出曲轴的质量中心线后,在曲轴两端加工出中心孔,使其两端加工出中心孔的轴线与曲轴的质量中心线重合。采用质量中心孔定位加工曲轴的主要优点为:减少曲轴动平衡时的去重量,提高动平衡的合格率,降低去重工序的加工节拍,改善曲轴内部质量补偿,但质量中心孔的设备价格昂贵,且设备大都需要进口。
2.2 轴颈的粗加工
传统的加工工艺设计时,曲轴主轴颈及连杆轴颈的粗加工都采用多刀车削工艺,即同时使用多把刀具一次完成轴颈的粗加工。曲轴车削机床采用多刀径向切削轴颈的方式,效率较高,但存在变形大、加工精度低、柔性差等缺点。
由于多刀车削受到加工精度低和柔性差的影响,已逐步被后来开发出的 CNC车削、CNC外铣和CNC内铣、车-拉工艺所淘汰。
CNC曲轴内铣机床是70年代开发的曲轴加工新机床,内铣的加工方式是:当装有硬质合金刀片的内铣刀盘高速旋转径向切入至轴颈尺寸后,刀盘环绕轴一周完成曲轴扇形面、轴颈、圆角、轴颈的铣削。机床带有中心架,可在一次安装下,依次铣削出所有主轴颈、连杆颈,由于各轴移动均为数控,因此机床具有极大的柔性,适用于多品种生产,铣削过程中多个刀片参与切削,铣削力小,因而曲轴弯曲变形小,加工精度高。
内铣加工
2.3 轴颈的精加工
曲轴是以两端孔定位的轴类零件,工件两端中心孔的几何形状、粗糙度的好坏在加工过程中都会影响到轴颈精加工的质量,而且在粗加工过程中,中心孔也会受到破坏,因此,曲轴在精磨之前往往都会增加一道工序,对粗加工后的中心孔进行修正,以提高磨削加工质量。
曲轴是发动机中的重要零件之一,技术要求也较高,其轴颈直径公差一般为IT6级公差,轴颈表面粗糙度为 Ra0.4~Ra0.2,因此为保证产品质量要求,曲轴在经过粗加工后,必须对所有轴颈进行磨削的精加工,以提高轴颈精度和降低表面粗糙度。曲轴轴颈传统的磨削方法分半精磨和精磨两个阶段,但随着毛坯制造技术的发展和粗加工设备加工精度的提高,目前大多数曲轴加工厂已取消了半精磨工艺,这样可以缩短曲轴的加工流程,同时也降低了曲轴的生产成本。
曲轴磨削加工
普通外圆磨削方式适用于曲轴主轴颈的磨削加工,而无法实现连杆颈的加工,传统的连杆颈的加工常采用偏心夹具定位夹紧加工连杆颈,但这样设备的柔性较差,加工精度较差,目前随着机床制造技术的发展,连杆颈的磨削则采用跟踪磨削法。跟踪磨削法是以主轴颈中心线为回转中心,一次装夹依次完成曲轴连杆颈的磨削加工(也可用于主轴颈磨削),磨削连杆轴颈的实现方式是通过CNC控制砂轮的进给和工件回转运动两轴联动,来完成曲轴加工进给。跟踪磨削法采用一次装夹、在一台数控磨床上依次完成曲轴主轴颈和连杆颈的磨削加工,能有效地减少设备费用,降低加工成本,提高加工精度和生产效率。
磨削完成后需对轴颈和圆角进行抛光,以降低轴颈的表面粗糙度,提高表面质量,曲轴抛光根据磨削表面质量以及产品要求,采用不同粒度的砂带进行抛光。
曲轴砂带抛光
2.4 曲轴油孔加工
曲轴油孔一般孔径较小、深度较深,属深孔加工,因此加工难度较大,曲轴油孔加工昀早采用摇臂钻加工,内壁质量较差,刀具寿命较低,工人劳动强度大,无法满足大批量加工需求,后逐渐被组合机代替,虽说可以满足大批量生产需求,但是设备柔性较差,刀具寿命也相对较低,目前已逐渐采用枪钻加工,枪钻用来加工深孔的深度一般可以做到枪钻直径的 100 倍以上,另外枪钻加工可以达到的精度很高,视不同的被加工材料和选用不同的切削用量可以一次加工出精度很高的孔。
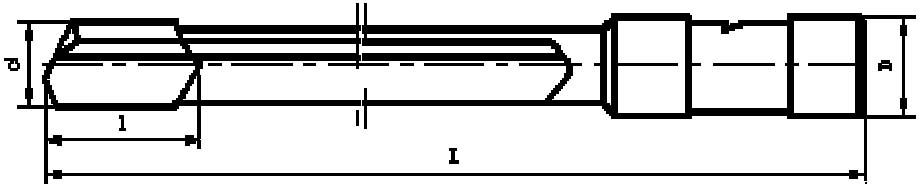

枪钻
2.5 曲轴强化工艺
为提高曲轴的强度、增加表面耐磨性,曲轴一般需要对轴颈表面、圆角等处进行强化处理,常用的强化工艺有淬火、滚压、氮化等,由于淬火适应范围广、效率高、强化效果好,因此淬火成为目前主要的强化工艺。
感应淬火
3、曲轴加工工艺过程虽然曲轴的品种较多,结构上一些细节有所不同,但加工工艺过程大致相同。
序号
|
工序内容
|
常用设备
|
1
|
铣端面打中心孔(毛坯厂加工)
|
专机
|
2
|
毛坯上线、检查
|
|
3
|
车止推轴颈外圆
|
专机或数控车
|
4
|
粗磨止推轴颈外圆
|
外圆磨床
|
5
|
主轴颈粗加工
|
专机或数控车
|
6
|
两端轴颈粗加工
|
专机或数控车
|
7
|
连杆颈粗加工
|
万能设备配偏心夹具、专机、外铣或内铣机床
|
8
|
油孔加工
|
万能设备或专机
|
9
|
中间清洗
|
清洗机
|
10
|
热处理
|
专机或专用工装
|
11
|
校直
|
专机
|
12
|
止推面磨削
|
专机
|
13
|
轴颈磨削
|
专机
|
14
|
两端螺纹孔、定位销孔加工
|
专机或加工中心
|
15
|
铣键槽
|
万能设备或专机
|
16
|
动平衡
|
专机
|
17
|
探伤
|
专机
|
18
|
抛光
|
专机
|
19
|
清洗
|
清洗机
|
20
|
下线检查
|
|
|
在关键工序常配备专用量具对加工质量进行检测。(中国工程机械动力部件网)(下一篇凸轮轴加工工艺)